The FDM technology, also known as Fused Filament Fabrication (FFF), falls under the material extrusion type of 3D printing technology. It is the most widely used 3D printing technology across the world.
FDM 3D printing uses thermoplastic polymers like PLA, ABS, PETG, TPU, etc. in a filament (wire) form that is extruded and deposited in the shape of the final object as required. The printing happens in a layer-by-layer form.
Popularly there are two types of FDM 3D printers, namely Cartesian and Delta 3D printers. Both of these types have different advantages and limitations.
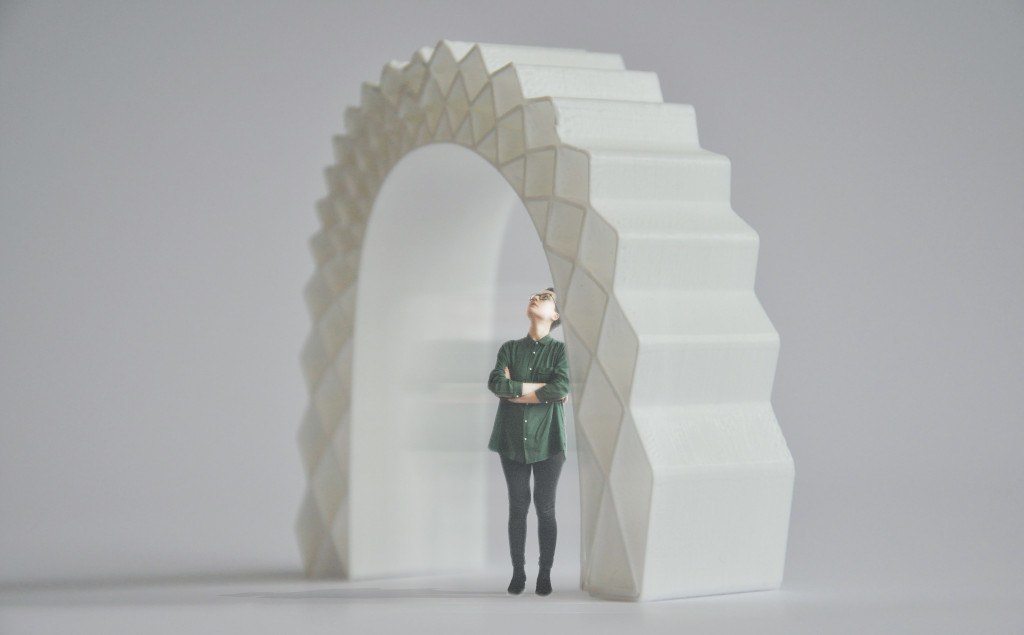
3D Printing Shops 3D Printing Service FDM – Fused Deposition Modeling
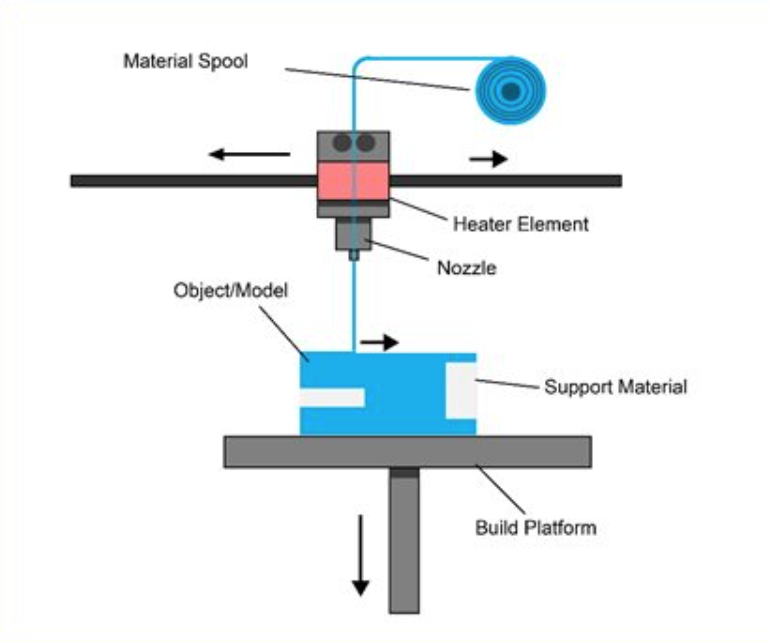
3D Printing Shops 3D Printing Service FDM – Fused Deposition Modeling
COMPONENTS OF AN FDM 3D PRINTER
Extrusion Head: It is also known as an extruder, it is one of the most important components of an FDM 3D printer. The extruder is an assembly of three sub-components like an extrusion system, heater, and the nozzle. All three sub-components work in tandem with the extruder.
The extrusion system pulls the filament into the heater, which heats the filament, and the nozzle then deposits the heated material onto the build platform.
Filament: This is the thermoplastic material in a wire/filament form wound around a spool.
Build Platform: It is also called Build plate or Bed. The material is deposited onto the build platform. Depending on the 3D printer, this build platform can either be cold or hot.
WORKING OF AN FDM 3D PRINTER
The FDM 3D printing process starts with the feeding of the filament into the extruder assembly through the extrusion system. The filament passes through to the heater in the extruder assembly. Here the filament is heated to a pre-defined temperature depending on the type of filament whether PLA, ABS, or PC.
Once the ideal temperature is reached, the material is then made to pass through the nozzle. The nozzle then moves according to the G-Code of the model created in the slicing software. The nizzle traces the geometry of the design.
The nozzle deposits the semi-liquid material onto the build platform and prints the cross-section of the model. One cross-sectional print refers to one layer. Once the first layer is completed, the build platform drops down by an amount equal to the layer height. The nozzle then springs into action again and it prints the second layer on top of the first layer in a similar fashion.
This process continues until the entire object is formed.
Once the 3D printing process completes, the printed object needs to be removed from the build platform. Supports, if any, also need to be removed and thus the final object is ready.
Post-processing, if needed, is then carried out on this final model
Pre-Printing
This is the stage where the 3D CAD model is created and then passed through a slicer software to convert the model into a machine-readable format.
3D Printing
The Multi Jet Fusion printing process starts with the scrapper depositing one layer worth of powder onto the build platform from the powder chamber. Once the powder is evenly spread on the platform, the liquid binding agent is jetted selectively to fuse the particles of the first layer. This is followed by spraying of the detailing agent onto the areas close to the fused areas. The detailing agent prevents thermal bleeding and maintains the surface quality and finish.
The process continues with the movement of the heating lamps over the build platform. This heats the liquid agents and helps in the complete fusing of the layer thus printed. This completes the first layer of printing.
This entire process is then repeated again and again till the entire object is 3D printed in a layer-by-layer form.
Post-Printing
Once the object is printed, the parts are left in the build chamber where they are allowed to cool down for some time. The object is removed afterwards and is de-powdered with the help of air blasts. And thus the final MJF 3D printed product is obtained.
MATERIALS – HP MULTI JET FUSION
The Multi Jet Fusion (MJF) technology was initially launched with only a handful of materials, mainly nylon. But since the launch, it has focused on developing new materials through in-house expertise and its material partners like Evonik, Arkema, Henkel, BASF, and others.
We look at some of the materials used on HP Multi Jet Fusion.
HP 3D High Reusability PA 11: One of the first materials to be made available with the technology. It is ductile and delivers quality parts.
Currently available through Instant Quote
HP 3D High Reusability PA 12: Also one of the materials made available from the launch. It produces strong parts at a low cost.
HP 3D High Reusability PP15: Developed by BASF. It is ideal for functional parts as it exhibits good chemical resistance, has low moisture absorption, and is easily weldable.
Ultrasint® TPU01: A flexible material developed by BASF
VESTOSINT® 3D Z2773 PA 12: The first-ever certified material for HP Jet Fusion 3D printers9. A multi-purpose affordable thermoplastic material for the production of strong parts, enabling the design of lightweight structures with great colour uniformity.
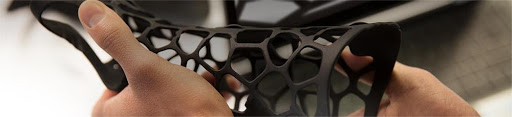
Materials used in HP Multi Jet Fusion/Courtesy: HP
TECHNOLOGY – HP MULTI JET FUSION
HP’s Multi Jet Fusion technology finds applications in a wide range of sectors and multiple areas of manufacturing.
Functional Prototyping
MJF is an ideal technology to be used for creating complex functional prototypes. It can easily mimic the utility of the original parts to be manufactured, it delivers dimensionally accurate products, and the parts are tough that can withstand tests like wind tunnel testing.
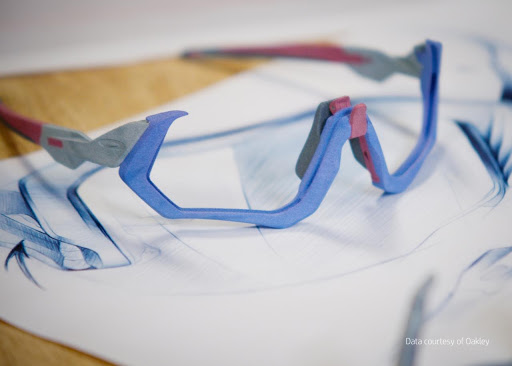
Rapidly iterating design ideas with HP MJF/Courtesy: Oakley
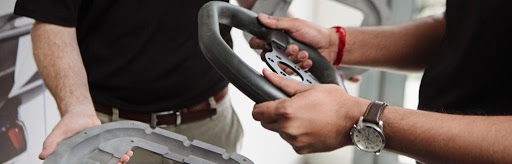
Tooling jigs and fixtures for automotive industry/Courtesy: HP
Manufacturing Aids
HP MJF parts can be easily customized and are tough and durable. The availability of a range of materials also helps in creating manufacturing aids like jigs & fixtures, maintenance tools, assembly tools, etc., that can withstand heavy loads.
End-use Products
MJF technology is capable of manufacturing end-use parts for all types of industries and applications. It can be used to manufacture products in aerospace, automotive, sports, footwear, industrial applications, healthcare, prosthetics, etc.
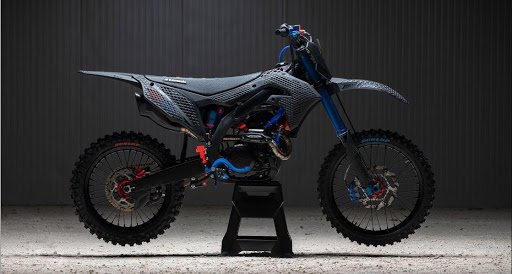
Kawasaki KX 450 3D Core motorbike/Courtesy: Skorpion Engineering
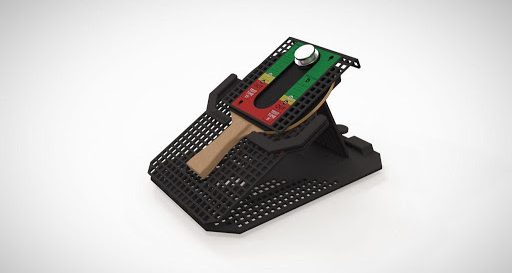
Low-Volume manufacturing
MJF is perfect for low-volume production. The MJF technology uses a powder bed and thus it is possible to manufacture different types of products in a single bed. By carefully arranging the parts to be printed, a significant amount of parts can be produced in one go. This suits low-volume manufacturing.
The classic applications lie in aerospace, vintage cars, spare parts, sports vehicle parts, etc.
Bridge Manufacturing
Bridge manufacturing refers to the concept of using 3D printing technologies to rapidly manufacture products when the production lies between product launch and full-scale manufacturing. This helps in faster time-to-market. The bridge manufacturing continues only until the traditional tooling (dies and molds) is manufactured.
Bridge manufacturing is generally employed to introduce new products in the market at a rapid pace.
Customization
HP Multi Jet Fusion technology allows a level of customization never seen before. It worked with a Spanish doll maker, LookReal, to create customized dolls that were unique to each consumer. Through traditional methods, that was difficult to create as all people have different sets of features. But it was made possible by using the HP MJF technology.
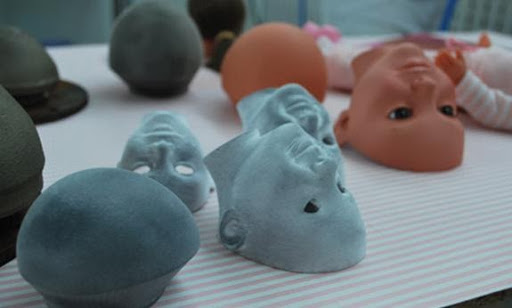
LookReal dolls were made with HP Multi Jet Fusion technology/Courtesy: HP/YouTube
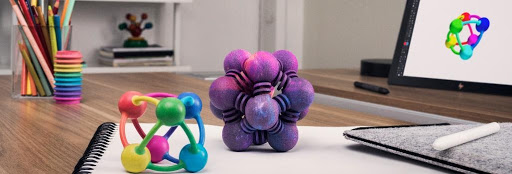
Functional and full-color products can be manufactured/Courtesy: HP
Full-Color Applications
HP also delivers full-color 3D printing solutions. It overcomes existing color limitations in 3D printing and helps innovation in product development for both prototyping and production.